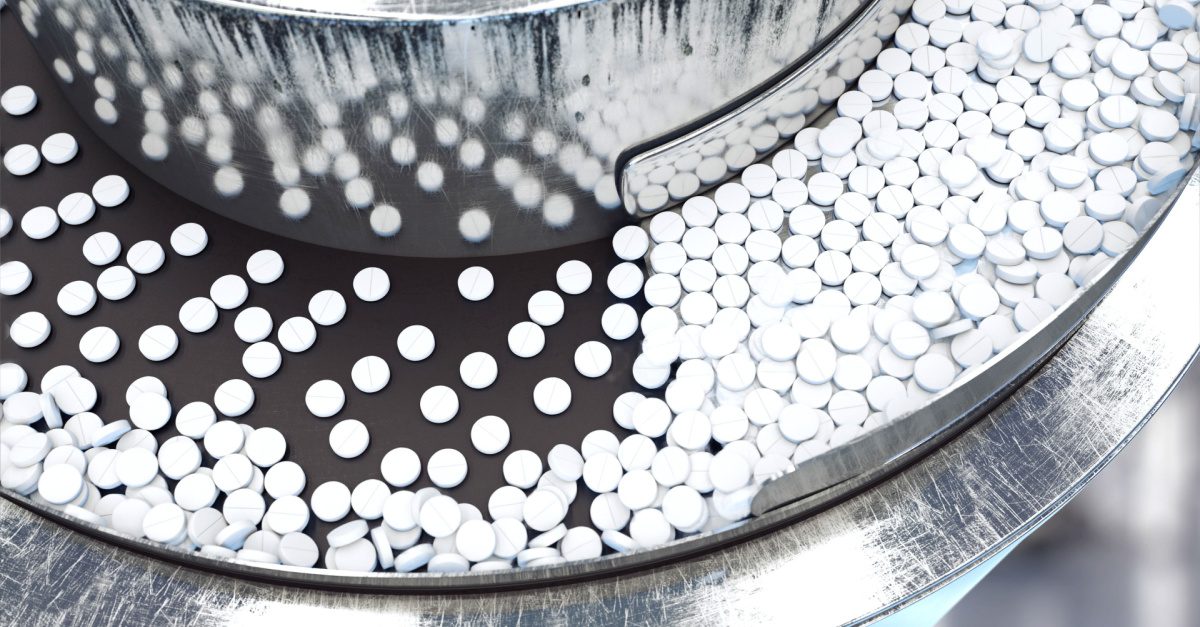
Manufacturing costs are important for every company that manufactures goods to sell. The calculation of the manufacturing costs is important for a company so it can make accurate pricing decisions, whether the new item should go into production or whether an item in the current catalogue should be discontinued. There are several manufacturing costs that companies will incur. Not all companies will have the same costs, but it is important to include all costs when determining the overall cost of a product.
Manufacturing Costs
A company that manufactures goods to sell to customers will initially purchase raw materials or components and use employees or labour in the manufacturing process. As well as these costs, there are several other costs that a company has in the manufacturing process. For manufacturing companies, there are non-manufacturing costs that will be incurred outside of the manufacturing process.
Inventory Accounts
Manufacturing companies will use three types of inventory accounts: Raw Materials Inventory, Work in Process Inventory, and Finished Goods Inventory. These accounts refer to the stored inventory in the warehouse, which can be raw materials and components, items that are not finished but somewhere in the manufacturing process, and the finished goods that are sold to customers.
Direct Costs
Product costs are referred to as either direct or indirect. A direct cost can easily be associated with a certain product. These will be direct labour costs and direct material costs.
Direct Labour Costs
It includes the work-related expenses that can be attributed to the manufacture of a company’s products. With companies in the service industry, direct labour cost is associated with the labour costs needed to provide a particular service. It is important to understand that direct labour cost does not involve labour that is not involved in production. However, it does only include the labour of employees who have been involved in the responsibility for setting up as well as maintaining the equipment.
To measure direct labour costs, a company should include all the manufacturing expenses in the equation. This will include all employee salaries and benefits, such as social security costs paid by the employer, unemployment-related taxes, pension or 401(k) expenses, all expenses related to medical benefits, and worker’s compensation-related insurance.
The direct labour costs should also include any costs of recruiting and training workers involved in the manufacturing process.
To calculate the direct labour costs, a company has to define a standard rate. This rate is an estimation of what a company expects the direct labour cost would be in normal operating conditions. There are two components of the model; the estimated cost of one hour of direct labour and the number of hours that are spent in producing an item. For example, if a firm’s total direct labour cost for one hour is ten dollars and it expects to use two hours on every single item during the manufacturing process, the standard cost of labour would be $2000, if the company manufactured one thousand units per week.
However, this calculation is only for normal manufacturing operations. If there are variances, specifically in the efficiency of the labour in the manufacturing process, this can cause a change in the direct labour cost. If the process is more efficient, the labour cost is reduced, i.e. by using new technology, while any problems in the manufacturing process can increase labour costs.
Calculating the labour costs involved in the manufacture of an item is needed to price an item for a customer correctly. If a company does not do this, then the price they set for an item could lead to a company not recovering its costs from the manufacturer of the product. If the price is set too high, then the item will not be competitive and not sell.
Direct Material Costs
This cost refers to raw materials that are part of a finished good and are easily traced back to that item. For example, if a company makes vacuum cleaners, a serialized electric motor can be traced back to the vacuum cleaner. Like direct labour costs, direct material costs are considered to be variable costs. This is because the total cost of direct materials increases as more finished goods are manufactured.
Manufacturing Overhead
Manufacturing overhead includes all the indirect manufacturing costs. It includes the indirect costs of getting the products ready to sell to customers. Manufacturing overhead costs consist of indirect labour, indirect materials, and factory-related costs.
Indirect Labor Costs
These are expenses that affect the company as a whole and not just a single manufactured product. Indirect labour costs are sometimes referred to as the real costs of doing business. These costs include such things as advertising employees, marketing employees, accounting, and payroll staff. These costs make up the overhead of maintaining the entire company and not just costs associated with manufacturing a product.
Like direct costs, indirect costs can be fixed and variable in amounts. Fixed costs include things like the rent or mortgage payments made for a company’s facilities. Variable costs include items such as electricity costs and fuel costs.
Indirect Material Costs
These costs include factory supplies such as MRO items and other factory-related supplies that do not directly become part of a product.
Factory-Related Costs
These costs are associated with facilities and are considered manufacturing overhead costs. These costs will include rent, insurance, equipment depreciation, utilities, and maintenance.
Period Costs
These costs are not considered to be associated with the manufacture of the finished item. There are a great number of period costs, such as shipping, accounting, research and development, advertising, and marketing. Period costs can be fixed or variable. For example, accounting expenses may be a fixed cost, but advertising may be variable depending on the type of campaign.
About the author: Nicholas Parker is an essay writer on kingessays.com and a content contributor to other sites. He used to track the manufacturing process at the company he worked for; nowadays, Nick is working out new ways of sustainable living and attends yoga classes to keep fit and be healthy.
From introductory production planning and scheduling training to advanced types of manufacturing operations, the IoSCM Manufacturing and Production Academy offers qualifications from Level 2 to Level 7. Not sure which course is for you? We promise to deliver outstanding support from the very first call—get in touch today. Call 0800 1422 522 or Email info@ioscm.com.