IoSCM Education Team
We have some of the best tutors in the industry as members of the IoSCM education team. When you have enrolled onto an IoSCM course you’ll receive unlimited one-to-one support, guidance and feedback from your assigned tutor.
Communication can be organised through a phone call, email, text, video call or through the chat system on the online learning platform.
Because we have tutors specialising in every sector of the supply chain industry, we have a strong understanding of the requirements to succeed and progress within every field.
IoSCM Learning Support Team
In addition to the tutor team, you will be assigned a learning support advisor who will ensure your learning journey goes to plan. They will introduce you to your course, help you navigate the learning platform and have frequent catch ups with you throughout your studies to make sure you’re on track.
Dedicated Business Support
If you’re an employer looking into training courses for employees, you will also have a dedicated business contact who can help you with finding the best training options based on your business requirements. Your business contact will also provide access to your employees’ course progression updates.
Our Client Base
Don’t just take our word for it; we’re trusted by thousands of businesses who have employees studying our distance learning courses, in 101 countries across the globe. From entry-level personnel to senior managers, we’re securing the future of the logistics and transport industry by delivering fully accredited UK qualifications.
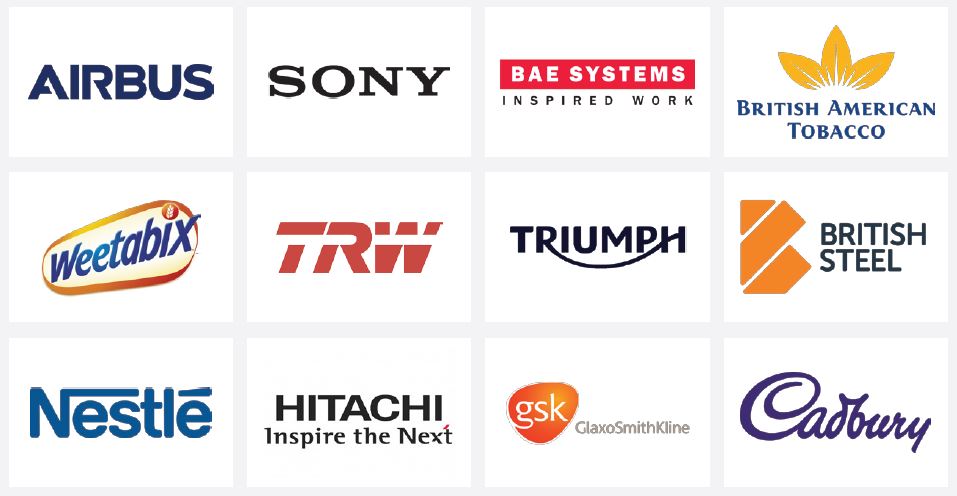