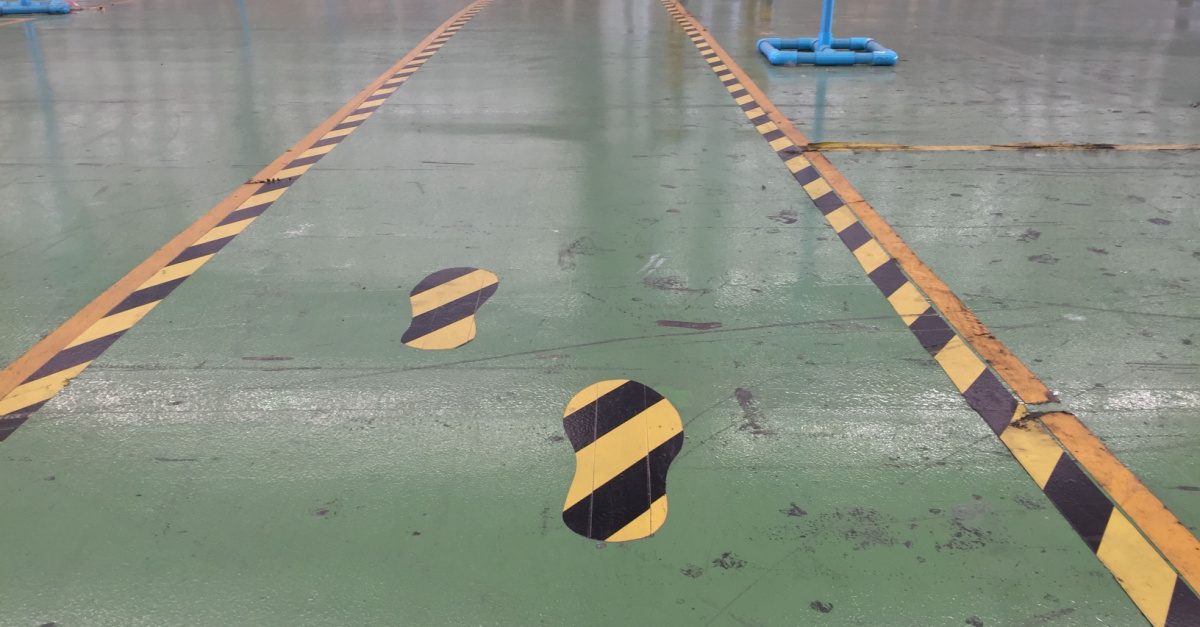
Transloading Problems To Strengths – 4 Uniquely Simple Ways To Improve Warehouse Safety
The heavy machinery, limited spaces, and continuous movement of goods make warehouses accident-prone locations. According to RIDDOR, the transport and storage industry’s fatal injury rate is at 0.9 per 100,000 workers, which is twice as high as all industries’ average for the five years between 2017-18 to 2021-22. These numbers are concerning for an industry that heavily relies on manual labour. Here are four simple but effective ways you could improve safety at your warehouse and change your transloading problems to strengths.
1. Personal responsibility for safety
Warehouse safety has to start with workers taking safety into their hands. While the management has to create a safer warehouse, it’s the workers who must ensure they take precautions and follow the safety guidelines required for the given task. For example, different tasks in the same warehouse may require different personal protective equipment (PPEs). The employer must provide appropriate PPE to each worker, but it’s also the worker’s responsibility to always have the proper safety equipment on for the task.
Warehouses are dynamic workplaces and require workers to be cautious at all times to avoid any mishaps. There are various responsibilities that workers should fulfil at warehouses. For example, workers must be physically and mentally healthy to keep themselves and others safe. If a worker has a medical condition or is on medications that make them sleepy, they should ask to get shifted to a different task. Workers must ensure the task they’re performing doesn’t put any of their co-workers or visitors at risk.
Management can also do their part to promote personal responsibility by creating and enforcing rules. Making wearing PPE at all times and following the markings on the floor mandatory are good examples of such rules. Any worker who breaks such rules should be penalised, and those with the best record should be rewarded as well.
2. Designing and maintaining a safe warehouse
A keyway to make a warehouse safer is to design it for safety. Designing a layout with adequate space for workers and vehicles to move around with goods can directly reduce the possibility of accidents. The warehouse floor should have no irregularities which could lead to workers stumbling or vehicles getting into an accident.
Another important part of warehouse design is the use of visual safety signals where possible. Safety signages, markings on floors, and posters on walls help keep safety in the mind of workers at all times. While it might not seem as useful, giving workers visual cues every day is an effective way of creating habits.
Marking all the areas with their names and safety warnings prepares workers before entering a new zone. A common but effective practice in the industry is marking safe walkways. These walkways should be easy-to-follow and visible at all times. More than just visual signs, the warehouse should prefer physical barriers where possible to keep workers at a safe distance. This is especially vital in areas with a greater risk of humans encountering machines or vehicles.
Warehouse designing is what creates a safe warehouse but to keep it safe the warehouse has to be maintained regularly. The first check for warehouse maintenance is cleanliness. A clean warehouse is a safe and healthy warehouse. Cleaning also highlights any irregularities on the warehouse floor which could lead to accidents. Walkways, electric cables, signages, safety equipment, and heavy machinery like forklifts should be maintained to ensure they’re functional at all times.
3. Extra caution with heavy machinery
Modern warehouses utilise heavy machinery like forklifts, aerial lifts, scissor lifts, and automated storage and retrieval systems. Such machines require caution while working with them anywhere but warehouses require workers to be far more cautious as the margin of error is much smaller.
To ensure worker safety with heavy machinery, they must be aware of how to operate the machines and the risks involved with operating them. To achieve this, the management must run training programs for workers that keep them updated with the latest features and best practices. The trained workers should be tested for knowledge and health. Only after they pass such tests, should they be allowed to work on the respective machine. These tests should be carried out at regular intervals to ensure all workers are qualified for the machines they’re working on.
Forklifts are one of the most common machines in warehouses today and so are the accidents related to them. Workers operating them must be especially careful and aware of their surroundings. For safe forklift operation, only trained, healthy workers should operate them following the SOPs. Forklifts should not be overloaded in any case. The operator should warn workers in the vicinity of the machine before starting the operation and remain in the area defined for the machine operation.
As an everyday activity with heavy machines, operators should run maintenance checks on the machines. Apart from the human side, all the machines also need to be maintained regularly as per their maintenance schedule to avoid accidents due to breakdowns.
4. A culture of safety
Warehouse managers have to do more than just invest money in safety. As top management, their actions are much more effective on the psyche of the workers and leave a lasting impression. Management can create an environment and culture of safety by actively participating in safety initiatives.
The culture of safety is what brings workers to the table and motivates them to contribute to improving workplace safety. Ensuring safety is always put first and empowering workers to report any close misses or accidents is the key. Communication between floor workers and management also highlights issues and helps find solutions that work.
Conclusion
Warehouse managers must keep in mind that allocating resources is just the first step toward creating a safer warehouse. They must invest time in auditing different areas of the warehouse for safety. Taking inputs from the floor workers is always a good place to start finding areas of improvement in the warehouse. Working on the current issues and following routine safety checks is the way towards maintaining the warehouse safe.
At IoSCM, we offer five levels of UK and internationally recognised warehouse management online courses. We offer a modern, flexible approach to distance learning. Study short-term courses or extensive management strategy — you choose your own full or part-time approach with unlimited tutor support throughout your time with us. From inventory management to strategic warehouse planning, our online training systems for warehouse management equip supply chain professionals with the skills necessary to advance their career.