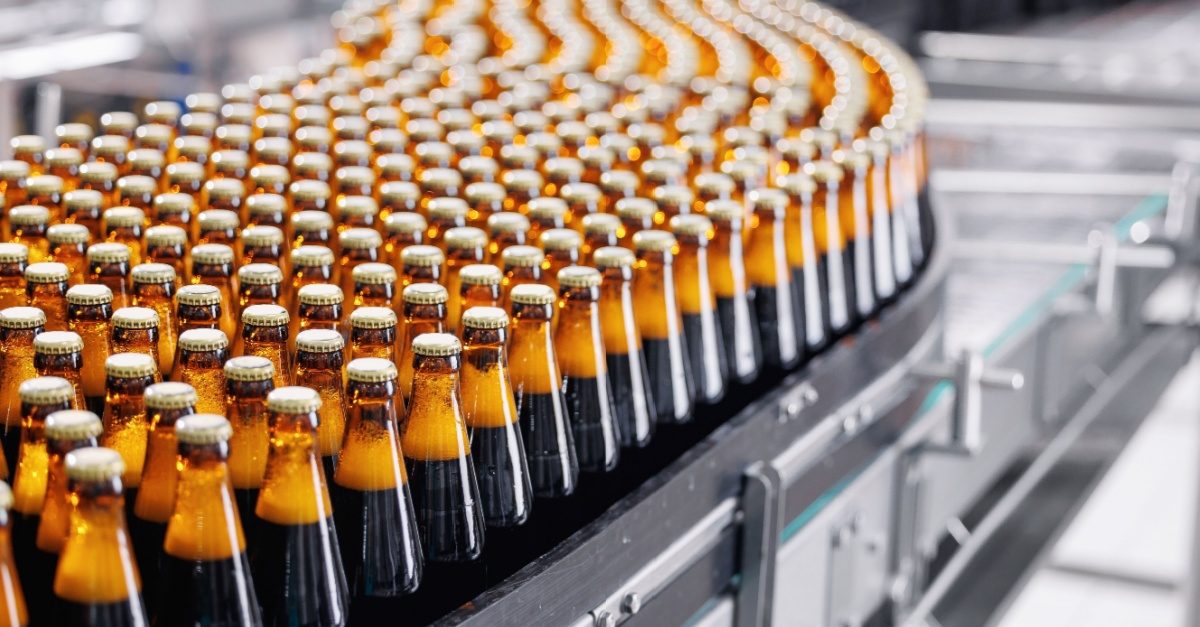
How to Reduce Waste in Assembly and Packaging
Factories lose millions of dollars daily as valuable materials go to waste. Metal scraps fall to the floor, excess packaging piles up, and defective products are thrown away. These waste materials harm the environment, eat into profits and push up prices for customers. The good news? You can avoid or reduce most of these wastes. Innovative manufacturers have already figured out how to dramatically cut their waste while saving money, helping the planet, and building better products at the same time.
So, how can you join these savvy manufacturers in reducing waste in assembly and packaging? Read on to find out!
Key Takeaways
- Waste reduction directly boosts profits, cuts costs, and improves product quality.
- Conducting a thorough waste audit is essential to pinpoint inefficiencies and target improvements.
- Optimising material selection and packaging design significantly minimises waste from the start.
- Streamlining assembly processes and adopting Lean principles drive operational efficiency and reduce scrap.
- Investing in technology and fostering clear communication across teams are crucial for continuous waste reduction.
- Designing products for waste reduction from the outset and implementing strong quality control prevents costly errors.
Leverage External Partnerships
Collaborating with specialised assembly and packaging service providers gives you access to targeted solutions that reduce waste and improve efficiency. These partners bring industry experience and focused tools that can solve problems without requiring large shifts in your current setup.
Many offer flexible options such as labour, equipment, or material resources tailored to specific points in your process. Whether it’s introducing sustainable packaging, using automation to cut excess, or helping rework a packaging line, their input often leads to noticeable improvements. These adjustments reduce material waste and increase speed and consistency across production.
Working with nearby providers that support local business growth can also deliver added value beyond operational improvements. These partnerships help shorten supply chains, reduce transportation emissions, and boost responsiveness without sacrificing quality. At the same time, they reinforce your commitment to sustainable practices while strengthening connections within your community.
Conduct a Thorough Waste Audit
Understanding your current processes is the first step toward reducing waste. A thorough waste audit helps teams examine each part of the process, from how materials move through the floor to how well final products meet quality expectations. Reviewing digital systems, material flow, and daily output offers a clear picture of where things slow down or go off track.
This kind of audit often highlights areas of packaging waste, overproduction, or poor layout planning. For example, teams might notice excess handling during assembly or frequent adjustments due to packaging that doesn’t match product dimensions. These findings bring hidden inefficiencies into focus and allow for thoughtful planning.
Accurate data makes it easier to spot issues in inventory management, streamline process design, and make better use of available resources. Teams gain a solid foundation for improvement and can begin targeting high-impact areas that lead to lasting change. A focused audit turns everyday observations into long-term gains.
Optimise Material Selection
Examining your materials is one of the most direct ways to reduce waste. Many facilities rely on outdated packaging designs or oversized components, which lead to excess material handling and unnecessary scrap. Switching to more efficient designs, lighter packaging, or recyclable inputs can lower waste without sacrificing quality.
It’s also crucial to work with suppliers who understand your goals. When vendors offer packaging materials in standard sizes that align with your production needs, it becomes easier to minimise cutting and avoid leftover pieces. For example, pre-cut liners or inserts can reduce overprocessing and support faster assembly.
Some facilities also benefit from take-back programs, where unused or surplus materials are returned to the supplier for reuse. This supports better inventory management and reduces landfill impact. With savvy sourcing and clear communication, companies can lower packaging waste while using resources more efficiently.
Streamline Your Assembly Process
Many forms of waste begin with a poor setup. Inefficient layouts, unclear work instructions, or repetitive motion often slow progress and lead to overprocessing. Reviewing the flow of tasks through layout planning or time studies helps identify friction points. Mapping each step makes it easier to eliminate delays and improve production line efficiency.
Visual tools and clear procedures give workers the structure they need. Standard operating procedures and checklists reduce confusion and support lean assembly practices. For example, positioning materials in a logical sequence can lower the chance of rework and reduce unnecessary handling between stations.
When each task fits into a consistent routine, assembly becomes more predictable and less error-prone. These improvements also help teams manage material handling more effectively and support better resource utilisation. Ultimately, consistent changes lead to lower scrap rates and smoother packaging transitions.
Use Lean Manufacturing Principles
Reducing waste begins with rethinking how each task adds value. Lean manufacturing helps identify which activities contribute to product quality and which ones drain time or materials. Value stream mapping is one method teams use to visualise the whole production flow. This tool highlights areas where overprocessing, material waste, or bottlenecks create inefficiencies.
Small, continuous changes often bring the biggest impact. Instead of relying on top-down directives, teams are encouraged to spot ways to simplify tasks or reorganise work areas. For example, moving tools closer to assembly stations or adjusting how components are packaged can reduce unnecessary motion and improve process control.
As lean practices take root, teams become more skilled at recognising signs of overproduction and poor resource utilisation. These habits support long-term cost savings and help maintain steady output. Over time, the entire system benefits from a more flexible and efficient approach to assembly and packaging.
Improve Packaging Efficiency
Packaging often contributes to waste in unnoticed ways. Oversized boxes, unnecessary fillers, and poor material choices can lead to excess packaging waste and higher transportation costs.
Selecting packaging materials that match the product’s weight and dimensions helps avoid using more than needed. For example, lightweight corrugated cardboard or moulded pulp can provide protection without adding bulk.
Another key area is the design of the packaging itself. Items that require custom inserts or awkward shapes often need extra material to stay secure. Switching to modular packaging or adjusting product dimensions to fit standard containers can reduce material handling and storage requirements. These changes increase packaging efficiency and support more sustainable solutions across the supply chain.
Invest in Technology and Automation
Technology can be a powerful tool in waste reduction. Manufacturing automation supports this by improving precision and reducing material waste during assembly. For instance, machines that cut packaging materials based on product dimensions help prevent excess trimming and reduce the volume of scrap. These adjustments improve production line efficiency and support more consistent output.
Digital systems also help track material flow and identify inefficiencies across multiple stages. Sensors can detect equipment wear before it causes downtime, and software tools can monitor packaging weight to prevent overuse of fillers.
These insights support continuous improvement by helping teams fix minor problems before they escalate. It becomes easier to control inventory, reduce overproduction, and respond quickly to waste-related issues.
Improve Communication Across Teams
Communication gaps can lead to costly waste during assembly and packaging. Teams may move forward with outdated instructions or incomplete information when updates aren’t shared clearly. A missed design change, for example, could cause the packaging team to use materials that no longer fit the product. That mistake often leads to scrapped materials, production delays, and lost time.
Shared dashboards, daily check-ins, or visual work instructions can improve department visibility. When each team understands what’s changing and when, they can adjust in real time. Better coordination supports lean manufacturing efforts and helps reduce errors linked to miscommunication.
Ongoing collaboration also makes it easier to improve material handling and reduce excess inventory. Decisions feel more aligned and proactive when production, design, and packaging teams stay connected. This helps prevent overproduction, avoid duplicate tasks, and support a more efficient assembly line from start to finish.
Build a Culture of Accountability
Shaping a workplace that focuses on waste reduction begins with leadership setting the tone. Clear direction, consistent expectations, and regular feedback help team members understand the importance of efficient material use and strong production line efficiency. When waste reduction becomes part of daily conversations, it’s easier to align decisions with sustainable packaging goals.
Teams are more engaged when they’re encouraged to take initiative. Workers who monitor their own material handling practices or suggest ways to improve layout planning contribute directly to continuous improvement.
Reinforcing accountability through small wins can also drive long-term progress. Recognising improvements in inventory management or rewarding teams that reduce scrap builds motivation. These habits make waste reduction part of daily routines and strengthen commitment across departments. Over time, a culture of ownership leads to better resource utilisation and more consistent production results.
Track Progress and Adjust Over Time
Even the best plans need to be reviewed and adjusted. Measuring results through key performance indicators gives teams insight into where improvements occur and gaps still exist. Metrics like material usage, packaging volume, and scrap rates help reveal how changes affect assembly and packaging efficiency.
Regular progress checks support continuous improvement and reduce the risk of falling back into inefficient habits. For example, if packaging waste drops after switching to right-sized materials, teams can explore other areas where material handling might improve. Reviews also make it easier to catch signs of overproduction or rising defect rates before they become larger issues.
Explore Reuse and Recycling Options
Reducing waste doesn’t always mean removing materials entirely. Many items left over from assembly or packaging can be reused or directed into recycling streams. For example, scrap cardboard from packaging stations can be collected and recycled, while leftover metal parts might be repurposed in other production runs.
Recovery efforts that support better resource utilisation can also be valuable. Components that no longer meet quality standards for one product might still serve a purpose in a different application. Some companies recover unused packaging materials or bulk items and return them to inventory, supporting lean manufacturing goals.
Designing clear systems for reuse and recycling makes these efforts easier to manage. Colour-coded bins, centralised collection points, and regular pickup schedules help streamline waste diversion. When systems are easy to follow and built into daily operations, reuse and recycling become natural parts of the production flow.
Design for Waste Reduction From the Start
Reducing waste starts at the design table. Engineers and product teams shape how materials are used, how parts come together, and how easily an item moves through production. Choosing recyclable materials, simplifying component counts, or aligning designs with standard packaging sizes can lower material waste and reduce overprocessing during assembly.
Early decisions also affect how products behave throughout their lifecycle. Items designed for durability, repair, or modular updates stay in use longer and create less demand for replacement. When packaging is considered from the beginning, it’s easier to avoid unnecessary bulk or excess cushioning that leads to packaging waste.
Designing with efficiency in mind helps limit rework and improves material handling during production. Teams that review assembly and packaging needs during the concept phase often find ways to streamline later steps. These choices support lean manufacturing, lower resource consumption, and help keep waste under control from start to finish.
Focus on Quality Control
Preventing waste starts with getting products right the first time. Components that don’t meet specifications or require rework create delays, increase material waste, and disrupt production line efficiency. Strong quality control measures help detect issues early, reduce scrap rates, and limit the need for adjustments during final assembly.
Visual inspections, testing checkpoints, and automated sensors can all improve process control. These methods support lean manufacturing by minimising overprocessing and helping workers catch defects before they move downstream. For example, flagging a misaligned part during subassembly can prevent an entire batch from being scrapped later.
Customer satisfaction is another benefit of consistent quality. When items arrive as expected and function properly, there’s less need for repackaging or replacement. That reduces packaging waste, avoids additional shipping, and protects your brand’s reputation.
Use Feedback to Drive Change
Consistent improvement often starts with listening. Feedback from production teams, inspectors, and even end-users can reveal issues that may not always be apparent in reports. For example, a worker may notice that a specific packaging material breaks down during handling, resulting in unnecessary repacking. Acting on these observations helps improve packaging efficiency and reduce material waste.
Feedback also helps identify areas of overproduction or unnecessary motion. If operators repeatedly flag the same inefficiencies or point out slowdowns in material handling, those patterns deserve closer attention. Gathering this input supports continuous improvement and helps fine-tune assembly processes for better results.
Over time, reviewing feedback trends highlights deeper issues that may need structural changes. Recurring complaints about packaging defects or delays in the production line can point to process design flaws. Addressing the root cause instead of applying short-term fixes leads to fewer disruptions, better resource utilisation, and stronger long-term waste reduction.
Conclusion
Reducing waste in assembly and packaging isn’t just about helping the environment. It’s about running a more profitable business. Every piece of scrap metal you prevent, every right-sized package you use, and every defect you catch early puts money back in your pocket.
The strategies in this guide work because they tackle waste at its source instead of trying to manage it after the fact. Start with the area costing you the most money and build from there. Over time, these efforts will lower costs, strengthen operations, and help you deliver better products with less waste.