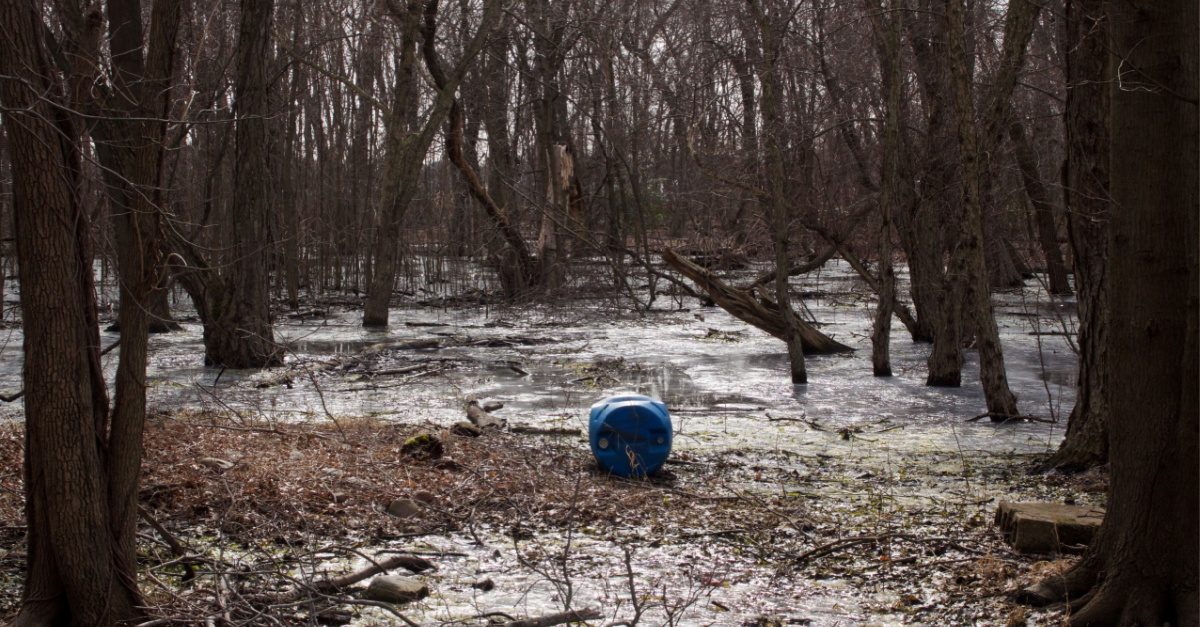
Phasing Out PFAS Will Cause Supply Chain Disruptions
Phasing out per- and polyfluorinated substances (PFAS) is necessary to protect the environment and public health, but also because it’s causing havoc in the world’s supply chains. PFAS is a critical group of chemicals used in businesses worldwide. Unfortunately, these “forever chemicals” are associated with serious health and environmental risks.
PFAS bans are forcing businesses to rapidly change how they operate and produce their products. The results are more significant and widespread than many realise. How is the PFAS phaseout disrupting supply chains? What can companies do to adapt?
An End to PFAS Manufacturing?
In December 2022, leading manufacturer 3M made headlines when it announced an end to its PFAS manufacturing activities. 3M plans to discontinue using PFAS in its products by 2025. This is one of the most high-profile cases of a growing trend: the phasing out of PFAS.
Businesses and manufacturers worldwide are rethinking their use of PFAS. This group of chemicals contains specific properties necessary for many products to perform as needed. Unfortunately, adverse health and environmental side effects caused by PFAS are leading to a rise in regulatory, legal and public demand for an end to its use.
Most businesses will try to support public health and sustainability when possible. From this perspective, phasing out PFAS is critical. The issue is that virtually every industry relies on a product that requires PFAS somewhere in its supply chain. Therefore, a sweeping end to production threatens the stability of millions of companies and the availability of their products.
Several PFAS bans are scheduled to go into effect in the U.S. in 2023, focusing on household goods and personal care products. The restrictions come amid an expanding list of lawsuits against businesses due to health issues and pollution resulting from PFAS products and manufacturing.
Businesses are now faced with a difficult choice. Those not removing PFAS from their processes and supply chains are vulnerable to liability lawsuits and compliance infractions. However, many products and manufacturing processes are not possible without PFAS.
Supply Chain Disruptions From PFAS Bans
How is the phasing out of PFAS impacting businesses? The main result is supply chain disruptions in numerous industries. Every sector and business uses PFAS differently, so finding alternatives is challenging. Manufacturers that abruptly end production of any PFAS-containing goods often leave companies at a dead end.
Continued Strain on the Semiconductor Supply Chain
A great example of the PFAS ban backlash is the semiconductor industry’s supply chain struggles. PFAS are integral to manufacturing chips and the equipment used to produce them. For example, they are crucial for photolithography and instill chips with several essential properties, such as heat resistance and high durability.
PFAS bans are increasing the cost of manufacturing semiconductor chips due to additional expenses, such as fines for regulatory infringement. Manufacturers attempting to reduce PFAS use may experience lower throughput as a result. Likewise, companies must devote time and money to finding alternatives to PFAS as soon as possible, distracting from regular operations.
As a result of these challenges, semiconductor supply chains are experiencing shortages and delays. The PFAS phaseout is coming at the tail end of the historic shortfall during the COVID-19 pandemic. This means many manufacturers and businesses have just recovered from one wave of supply chain disruptions only to be hit with another.
Struggling to Adapt to the PFAS Phaseout
The disruptions pose unique challenges for businesses relying on suppliers providing products with PFAS. The price-per-unit has increased since these products are not as available. Additionally, companies are seeing longer lead times on electronics due to supply chain disruptions.
One unfortunate consequence of these issues is an increase in counterfeit or low-quality alternatives. Businesses that need certain components but can’t afford the long waits and high prices from reputable suppliers may be forced to go elsewhere. This is a serious issue since counterfeit electronic components can lead to legal problems, compliance infringement, poor product quality and unreliable performance.
Consumers may also begin feeling the impact of PFAS bans. While reducing harmful chemicals is a good thing, businesses may be forced to increase prices due to supply chain disruptions.
Certain properties may be more difficult to produce without PFAS, and businesses must fund research and development (R&D) projects to find alternatives. Shortages and delays from suppliers due to bans will eventually trickle down to consumers. The phaseout will inevitably have negative side effects without affordable and effective options.
How Businesses Can Prepare to Phase Out PFAS
What can companies do to minimise the negative impact of the PFAS phaseout? Bans are daunting, and it’s natural for business leaders to be concerned. Adapting will take time, but there are steps that can help ensure a smooth transition.
For example, businesses can utilise a wealth of guidance from the U.S. EPA’s new chemicals review in response to the Toxic Substances Control Act. The EPA’s website covers the entire process for requesting testing and approval of PFAS alternatives, as well as contact information for getting assistance.
The EPA has also announced a new framework for approving certain PFAS uses that are deemed low- or no-risk. This program may relieve businesses that must use PFAS but aren’t necessarily harming people or the environment. It will also result in more research on the risks and how regulations can effectively quantify and categorise them.
Businesses can also adjust their product designs or suppliers to reduce their reliance on forever chemicals. Part obsolescence is rapidly becoming a top concern for many companies as they are forced to prematurely retire products or equipment containing PFAS. This could result in new supply chain disruptions due to a shortage of suppliers providing alternative products.
Businesses must research and connect with PFAS-free suppliers and manufacturers as soon as possible. R&D leaders should consider adapting product designs to strategically remove components that might traditionally contain or require PFAS.
However, buying mass amounts of equipment components containing PFAS before phaseout may not be wise. Depending on the expansion of bans in the near future, businesses may be forced to replace any PFAS-containing equipment, regardless of how recently it was purchased.
Finally, businesses must thoroughly understand the risks associated with PFAS and where these chemicals are in their supply chain. A lack of visibility is one of the biggest challenges with a widespread phaseout. Many companies are unaware that PFAS are present in their supply chains or that these chemicals have serious adverse side effects.
Utilising supply chain analytics and mapping technologies enables businesses to increase their supply chain visibility. A clear understanding of where every product, material and component comes from can reveal hidden sources of PFAS. Companies can more easily adapt to meet new regulations with this information readily available.
Moving Forward Without PFAS
PFAS have been central to countless supply chains since the mid-20th century. It will take time to adapt to a world without it. While this change is necessary to ensure public health and sustainability, a rapid phaseout of PFAS in manufacturing could trigger widespread disruptions.
Certain industries, such as semiconductor manufacturing, rely on PFAS and lack clear alternatives. Supply chain disruptions due to bans could lead businesses to experience delays, shortages and price increases. Some may even resort to utilising counterfeit products.
Businesses must be proactive to successfully adapt to a PFAS-free supply chain. It may be helpful to utilise EPA guidance, seek new suppliers, update product designs and increase visibility.
Stand out from the crowd, show your expertise with Certified status from IoSCM. Visit https://www.ioscm.com/certified-status/ to find out more.