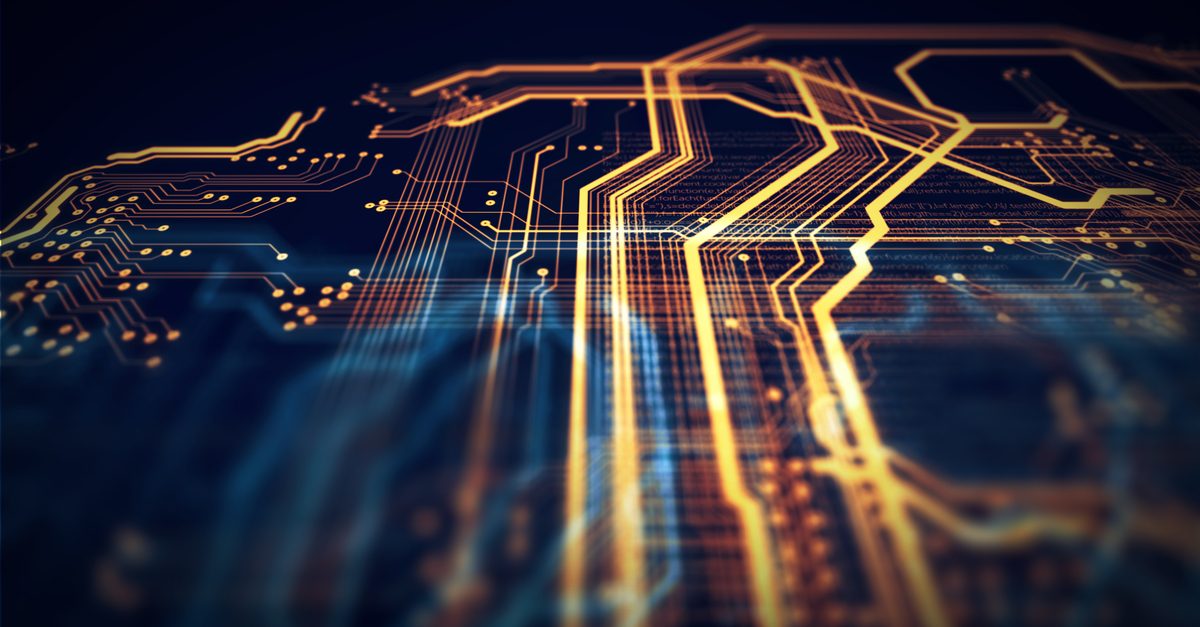
The Printed Circuit Board assembly process involves the placement and soldering of the electronic components on the bare board (Circuit Board minus the components) which can be accomplished either by manual assembly or Surface Mount Technique (SMT) line assembly methods. Surface mount technique involved soldering of components on the bare board, while other method involved drilling holes in the bare board, and that’s called through-hole assembly. Both through-hole and surface mount components can be soldered manually on a PCB. With the shrinking chip sizes and dense circuitry, SMT line assembly is the widely used PCB assembly technique today.
The automation of PCB assembly using the SMT line method brings speed and uniformity but the manual assembly has its share of unique merits which cannot be overlooked. Hence, it is essential to understand the advantages and disadvantages of both assembly techniques before choosing the right method for your PCB assembly.
Initially, through-hole components were exhaustively used in the PCBs until the demand for compact circuit boards increased in the electronics industry. The small board size couldn’t accommodate large through-hole parts and hence the Surface Mount components became popular. SMT parts are smaller in size and have leads that can be directly soldered on the PCB surface. They are cheaper than through-hole parts and offer better electrical performance. SMT passive parts have majorly replaced their through-hole counterparts already.
Through-hole parts are used in high-power circuits where large components are essential to handle the high-voltage, thermal, and mechanical stability requirements. In applications where PCBs are exposed to harsh environmental conditions like vibration, radiation, and extreme temperatures, through-hole parts are preferred. They offer robust connectivity by soldering the through-hole leads inside the drilled holes.
The different methods used for soldering the electronic parts on the PCB are manual soldering, wave soldering, and reflow soldering. Manual (Hand) soldering is the simplest method used in PCB assembly. The soldering iron tip is positioned above the joint and pressed against the component placed on the pad along with the solder wire. After removing the soldering iron, the solder joint hardens and establishes the connection. This method is also known as soft soldering. It offers a strong connection that can also be reworked later. Manual soldering is the best option to solder components that are difficult to access by huge machines.
Usually, through-hole parts are wave soldered and SMT parts are reflow soldered during PCB assembly. In the wave soldering method, the through-hole components are inserted in the drilled holes and a molten solder wave is applied to the PCB that connects the leads to the PCB holes. In the case of reflow soldering, the solder paste is applied to the pads and SMT parts are accurately placed using automated pick and place machines. Next, the board is run through a pre-heated oven which reflows the solder paste to make a solder joint between the leads and pads of the SMT parts. This process is faster and cheaper compared to the wave soldering method used for through-hole components.
Manual assembly depends on skilled technicians for the physical placement of components and uses the hand-soldering method. For low-quantity orders, the machine assembly will not be cost-effective. Manual assembly can reduce project delays as the assembly staff will visually inspect the PCBs for any incorrect footprints, misalignments, etc. A machine inspection may miss out on a few faults or even halt the assembly process for failures. But the manual process can quickly resume, as the technician can inspect and correct those mistakes on the spot.
An SMT line assembly is typically used for SMT parts assembly. It can be an automatic or semi-automatic process. SMT production lines have different flows based on the assembly requirements. Compared to manual assembly, SMT line assembly supports features like high density, high reliability, and low cost. It is a more efficient PCB assembly process.
Based on the requirement of a pick and place machine for complete automation or manual loading of the components, the SMT lines are classified as automatic and semi-automatic types. Several machines are used in SMT lines to enable complete automation of the assembly like Solder paste mixer, SMT loader/ unloader, Solder paste printing machines, and AOI machines.
The SMT line assembly has become a standard assembly method but has few exceptions. It is not suitable in applications like prototypes built for minimum quantities or boards with special components (like heat-sensitive, unique size or shape, etc) Through-hole components on small build volume (lesser quantity) PCBs are ideal contenders for the manual assembly process. Boards having press-fit components or custom parts may also require manual assembly. Components having longer lead times that have to be assembled separately can be handled by manual assembly methods.
A manual process can also be used to verify existing PCBs that are assembled using the SMT line method. Any rework or touch-up requirements for SMT parts can be done by manual soldering. During the automated assembly process, tiny SMT parts may get displaced or soldering defects like bridges (bridge is the connection of two or more pads’ unwanted connection, usually happened while soldering) might occur. The manual soldering method can attend to such SMT assembly issues for clean-ups.
The dependency on skilled technicians and chances of human error is high in manual assembly. The method cannot be used for large-scale PCB assemblies due to its excess time consumption. Certain components cannot be assembled using the manual method like dense SMT parts having pins beneath the chip, parts with fine pitch pins, and discrete components in miniature packages like 0201, 01005.
The increased complexity of circuits has made the PCBs very compact. Placing the tiny components closely is not feasible in the manual assembly process and hence SMT line assembly is used with automated pick and place machines. The SMT line offers high-speed assembly which can bring out the final product swiftly. This is a huge competitive advantage that has made the SMT automated assembly process a universally accepted method. Low cost, reduced faults, consistent quality, and miniaturization are other added advantages of the SMT line assembly.
Knowing these benefits and drawbacks, it is easy for you to choose the right assembly method for your PCB product. An experienced Contract Manufacturer can offer you a high-quality assembly service by using a combination of automated equipment and skilled technicians together.
Author Bio:
Ken works as a Sales Engineer at Technotronix. He brings 15 years of experience in printed circuit board sales and technical client service. Feel free to get in touch with him on Twitter.