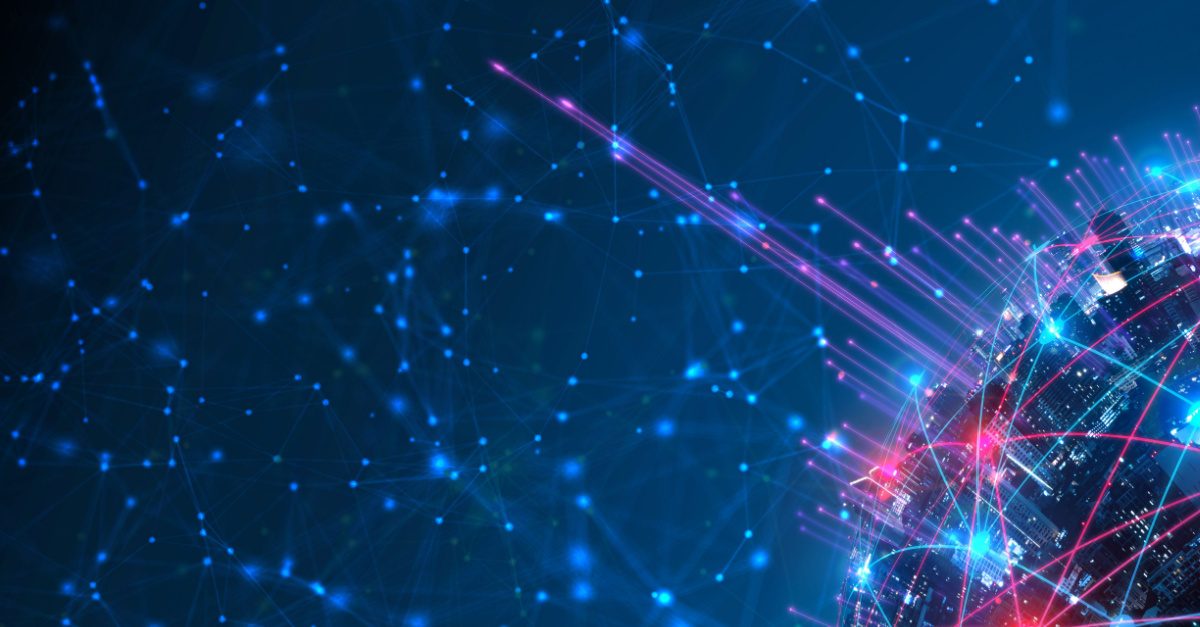
Communication is the backbone of successful business operations, especially in logistics. Despite this, it’s also the sector where many businesses continue to have difficulty. When one area in the supply chain fails, the others follow in a domino effect. The result is a cascade of issues ranging from minor ones, like mismatched placements, to major ones, like downtimes that take months.
This is why businesses always have to put good communication practices at the forefront of their efforts. The supply chain department is characterised as a fast-moving environment that, if your team isn’t equipped to keep up, it’s easy to get caught in a limbo of emails, unread messages, reminders, and calls.
Whatever the reason behind your communication, there are so many ways to fix them. Here are the latest ways to improve the way you stay in contact with every part of your supply chain.
Utilise The Latest Equipment
Nothing beats the improvement technology can bring to a business. Companies with the latest pieces of equipment can position themselves a few steps ahead of those without.
So, take the time to evaluate how your business, particularly the supply chain department, is doing in terms of integrating digitalised equipment.
Investing in the latest innovations may require a lot of canvassing, budgeting, and resources. But it also delivers powerfully in terms of returns. Not only will your supply chain operate at greater levels, but it also fosters continuous growth. This is because significantly improved communication reduces delays and margins of error.
A basic but much-needed upgrade lies in radio systems. The best ones offer a variety of features, like a 10 meter range, that work together to ensure clear, precise, and quick messaging at any point in the supply chain.
Of course, you can rely on supply chain management software. But it doesn’t really provide the level of real-time communication radios offer.
You can check out Stryker’s and many other radio providers to start your search.
Use Cloud-Based Communication Software
Alongside the latest hardware, your business must catch up in terms of software. Communication in your supply chain department can’t be cohesive when every member uses different networks to communicate. For firms that span multiple teams, a single, cloud-based network to streamline all daily communications ensures the best results.
It’s easier to track processes like arrivals, delays, pending orders, and inventory levels when every supply chain department member uses a single platform. The ideal ones even provide users with automatic notifications, keeping everyone on the same page.
Be Precise In Sending Communications
Whenever you send reports or contact people on the field, you must follow the best practices of logistics communication. Be specific with quantities and descriptions. If possible, you must use logs to keep all details precise.
You can easily address these concerns by investing in new communication software, as detailed in a previous point. Most businesses see a significant shift in growth when such turnkey solutions are utilised.
Practice Transparency With Your Team
Miscommunication also happens when there’s a lot of data withheld from the rest of the supply chain team. For as long as it isn’t confidential or classified, management teams should allow a reasonable level of access. The more transparent, the better.
This creates an environment of trust where open communication can prosper, whether it involves completing projects or addressing problems in your supply chain.
Start by talking to your team about where they could encounter regularly occurring bottlenecks. Say, for instance, you’re spending too much time nurturing certain suppliers at the expense of others. Or, resources aren’t allocated proportionately in each supply chain step.
With transparency, proactive action can be taken to address those concerns. In those examples, the team can make changes to fix issues before they cause serious trouble to the entirety of their operations.
Establish Clear Metrics
Setting clear metrics lets everyone in your supply chain know how to measure performance, make reports, track orders, and communicate as a whole. Miscommunication can be reduced when the terms used are uniform and the criteria are straightforward.
Each company will have its specific needs and standards, but a few universally used ones include:
- Quality performance: Usually measured by the number of defects per total number of individual item receipts
- On-time delivery performance: The ratio of on-time deliveries to total deliveries weekly or monthly
- Cost performance: The deviation (in percentage) from the standard cost for all items shipped by a particular supplier.
Apply these within the team and with your suppliers. This way, all the information shared regularly keeps everyone updated on what to expect. End-to-end clarity is key.
The Bottomline
A breakdown in supply chain communication can lead to massive losses in your operations. Fortunately, most of these problems are easy to fixable when you keep your business updated with the latest tools and practices. The strategies above are a few of those worth exploring for your business’s ensured growth. Reach out to the experts to learn more.
Advance your supply chain operations with IoSCM. Call 0800 1422 522 today to find out how we can help.