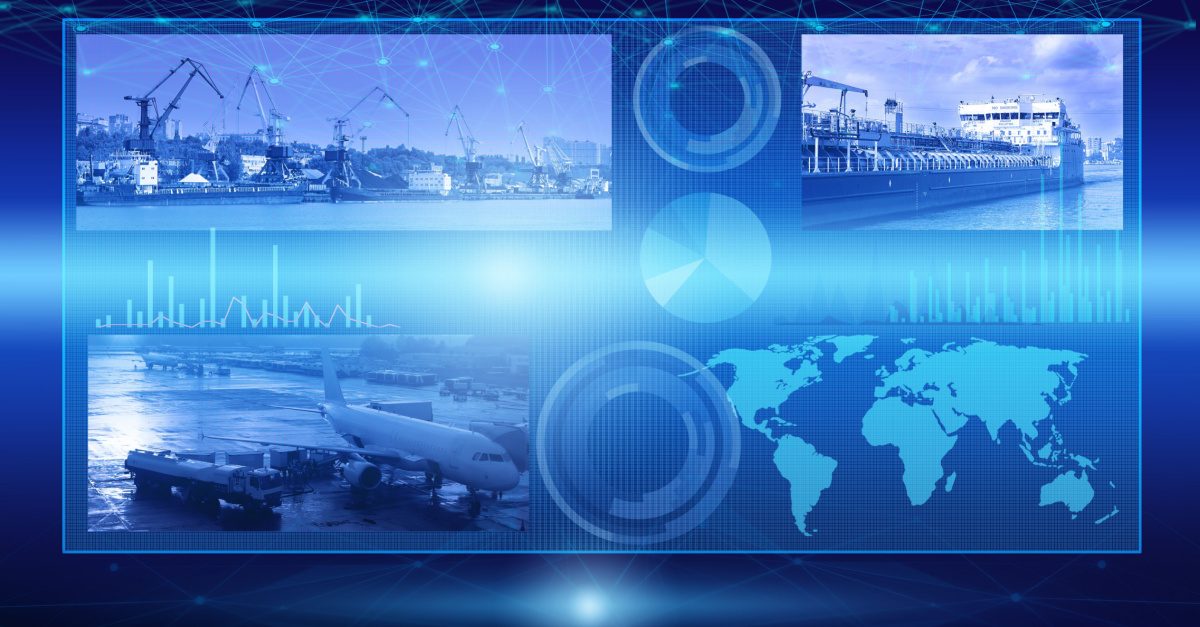
Automated Loading and Unloading Systems: A Look into the Benefits and Challenges of the latest trend in Logistics
Automated loading and unloading systems have become a critical component of logistics, particularly in the supply chain.
Businesses are resorting to automated technology to optimise their operations as demand for shorter delivery times and increased efficiency grows. In the Material Handling Industry’s 2023 Annual Report 76% of respondents said that they would be increasing their investment is supply chain technology and innovation. Additionally, John Paxton, MHI CEO, states “Responsible supply chains must react in real-time to changing conditions, this requires actionable data, automation and automated decision-making.”
This article examines various automatic loading and unloading systems and analyses the advantages and disadvantages of integrating them into logistics operations.
We assess the impact of these technologies on the industry and share insights on how you can make the best decision for your business.
So let’s look at these systems and how it can change the way things are delivered.
What is automated loading and unloading systems?
The process of loading and unloading goods into articulated lorries automatically involves the use of robots and other automated systems. This method is applicable in several industries such as retail, distribution, and manufacturing.
Type of Automated Systems
There exist various kinds of automated loading and unloading arrangements. The particular system implemented will be contingent on the distinctive requirements of the sector and the sort of merchandise being conveyed. A few frequent varieties comprise:
Automated guided vehicles (AGVs)
Automated guided vehicles (AGVs) are compact, self-driven machines that are utilised for transferring commodities within a storage facility or a dispatching hub. AGVs are capable of loading and unloading merchandise from articulated lorries.
Robotic arms
Robotic arms have the capability to transfer items onto or from articulated lorries. This technology can be utilised to load and unload a diverse range of merchandise, such as crates, pallets, and single units.
Conveyor systems
Conveyor systems can be employed to move commodities to and from articulated lorries. These systems can be employed to load and unload a range of commodities, such as boxes, pallets, and individual pieces.
As it is evident, these systems are an advantageous apparatus for enterprises that require swift and efficient movement of commodities. These systems can enhance efficiency, productivity, safety, and precision.
Benefits of automated loading and unloading systems
Efficiency & productivity
These systems can enhance effectiveness and output. Automated systems can load and unload commodities much faster than human labourers. This can curtail the transit duration for goods, resulting in quicker delivery schedules. Moreover, automatic loading and unloading systems can function non-stop. While human workers require breaks and leisure time, the automatic systems can operate round the clock. This can upgrade effectiveness and output.
Improved Safety
In addition, automatic loading and unloading systems have the potential to improve safety measures and reduce injuries. Human labourer’s are frequently exposed to injuries caused by lifting weighty objects or being hit by mobile machinery. Automated systems can eradicate these hazards, particularly in sectors with a substantial likelihood of injuries, like manufacturing.
Increased Accuracy
This can help reduce the risk of errors, leading to delays and disruptions in the supply chain. Furthermore, such systems can improve accuracy. In reality, they can guarantee that merchandise is loaded and unloaded in an accurate sequence and position. This can diminish the likelihood of mistakes, which might cause setbacks and disturbances in the logistics process.
Reduced Cost
Moreover, implementing loading and unloading systems can help curb expenses in various aspects. They can minimise the requirement of a manual workforce, resulting in savings on labour costs. Also these systems can also mitigate the possibility of harm to merchandise, hence leading to savings on material costs.
Challenges of automated loading and unloading systems
Initial investment
Purchasing and implementing these systems can be an expensive endeavor. Nevertheless, the potential for significant savings in the long run makes them a prudent investment.
Technology
These technologies can be inflexible. They may not be capable of accommodating all categories of merchandise or all sorts of loading and unloading scenarios.
Inflexibility
While these systems can handle most goods they may not be able to handle all types of materials or loading/unloading scenarios. Large, heavy, and oddly shaped cargo may be difficult for these systems to adapt to.
Maintenance
Regular upkeep is essential for the seamless functioning of automated loading and unloading systems. However, this upkeep can incur significant expenses, but it is imperative to guarantee the uninterrupted operation of the system.
Training
It is essential to provide proper training to personnel who will be handling automated loading and unloading systems to ensure safe and efficient operation. Although the training process may be costly and time-consuming, it is indispensable to guarantee the optimal functioning of the system.
Job Replacement
Automated loading and unloading arrangements may also result in unemployment. As these arrangements become more prevalent, they may substitute human labourers. This could result in job losses and financial difficulties in particular communities.
Conclusion
Ultimately, notwithstanding the obstacles, automated loading and unloading systems can prove to be an advantageous asset for enterprises that require prompt and efficient movement of merchandise. The selection between the deployment of automated or manual loading and unloading will hinge upon the particular requirements of the enterprise. Companies should consider the factors that hold the utmost significance for them, such as effectiveness, safety, precision, expenses, and adaptability.
About Us:
Castell Safety International is part of the Sentric group, which consists of three sister companies – Kirk in the US, Castell in the UK and STI in France. Sentric Group produces uncompromising safety solutions for businesses whose people and equipment operate in harsh and safety-critical environments.
From power generation and distribution, heavy plant works to loading bays and many industries in between, we believe everyone has the right to be safe at work.
For more information on Salvo logistic solutions, visit https://www.castell.com/our-products/logistics-solutions/or contact sales@castell.com to speak to a loading bay expert.
Help your business stand out from the crowd with Global Recognition. Submit your nomination(s) today for this years IoSCM Supply Chain Awards 2023.