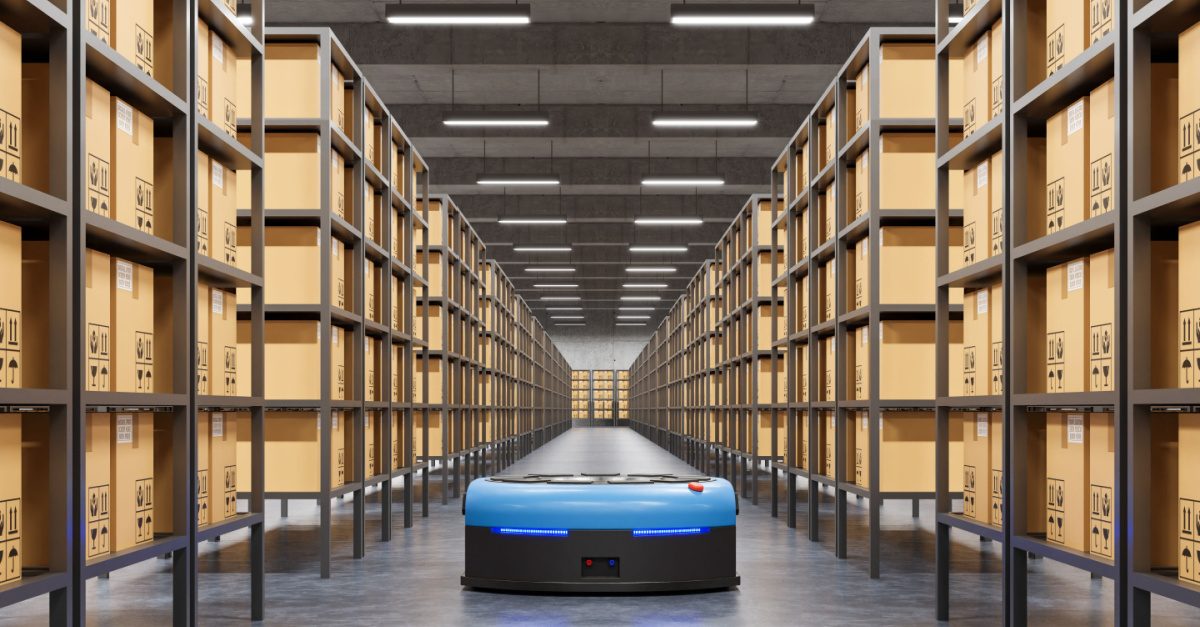
5 Proven Ways To Optimise Your Warehouse Operations
An efficient warehouse can help you reduce production costs while improving your profit margins. However, if your warehouse isn’t correctly set up and optimised, it might lead to inefficiencies, such as poor product fulfilment and increased wastage.
Improving your warehouse operations is essential to help increase productivity and minimise losses while storing goods. Meanwhile, optimising warehouse logistics ensures your company is shipping the right product to the correct location without delay. Delivery time has a massive impact on your business’s profitability.
Production delays may lead to increased inventory costs and wasted time and resources. Hence, finding ways to improve your warehouse operations’ efficiency is best. Doing so will give you more control over your inventory and avoid overproduction or underproduction.
The following are five practical ways to help your company optimise its warehouse operations:
Identify And Eliminate Production Bottlenecks
Before streamlining your warehouse operations, you must determine the bottlenecks that cause production delays. Obstructions can be costly for your business because they could affect customer satisfaction, stress your workers, or the quality of your products.
On the other hand, adopting lean warehousing is vital to reduce resource consumption. It can also help you determine less productive processes. Identifying areas with the most potential for improvement and developing new methods can help eliminate bottlenecks.
Identifying and eliminating production bottlenecks can help you use your existing resources efficiently without compromising productivity. This results in less stress among your employees, which could lead to lower turnover rates.
Streamline Picking Processes
Warehouse picking is typically one of the biggest challenges facing most companies today because there’s too much stuff in many places. This makes it hard for your employees to find what they need, affecting their productivity while increasing the risk of errors and accidents.
Streamlining your picking process is an excellent way to optimise your warehouse operations. You can invest in automation, such as conveyors or self-service kiosks. It’ll enable you to reduce manual handling and increase staff efficiency.
Also, developing picking routes will make it easier for employees to locate items on shelves and navigate the warehouse more efficiently. This way, you can reduce time spent looking for goods and improve productivity.
Invest In Storage Systems
You need a proper storage system if you only have boxes and containers to store your inventory. Doing so ensures your employees know where to place items according to their type and size, which helps expand warehouse capacity.
Meanwhile, consider a pallet racking system to optimise your storage. Pallets are known for their durability and strength, perfect for the warehouse environment. Aside from that, they come in various sizes, so you can choose what fits your business needs.
Organise A Warehouse Layout
A well-organised warehouse layout will help you improve storage utilisation, increase efficiency, and reduce operational costs. It also results in higher inventory accuracy, enhanced customer service, better product availability, and greater visibility for inventory.
You can create a warehouse layout by assigning zones for different stocks. Marking these zones will help employees know where to put specific products. This way, you can track items easily while maximising your storage space.
Avoid Overstocking Slow-Moving Items
Slow-moving items can be space-consuming as selling them will take significant time. In addition, you need to keep the inventory in stock until it gets sold. The problem with this is that there are chances for these products to get damaged or even expire.
Instead of stacking slow-moving items in your warehouse, consider replacing them with high-selling products. You should also monitor inventory demand to ensure you won’t have to produce more products with lower demand.
By reducing the stock of your slow-moving items, you can free up your warehouse space for other high-selling products. You can also reduce the costs of producing goods you may need help selling later.
Key Takeaway
Warehouse optimisation is a time-consuming process requiring careful planning and effort. But when you get it done, your business can cut costs, increase profits, and stay ahead of the competition. It can also help you find more effective ways to increase productivity.
Your warehouse operations may include investing in storage systems and eliminating the bottlenecks in resource consumption. In addition, you may have to improve your warehouse layout to make it easier for your staff to locate items. Ultimately, warehouse optimisation can help you improve your supply chain system, increase efficiency, and ensure business success.
Guarantee success in your industry with IoSCM. We offer every learner much more than just a qualification; we provide the opportunity to grow, learn and progress as a professional with our unrivalled support network. Call 0800 1422 522 today.