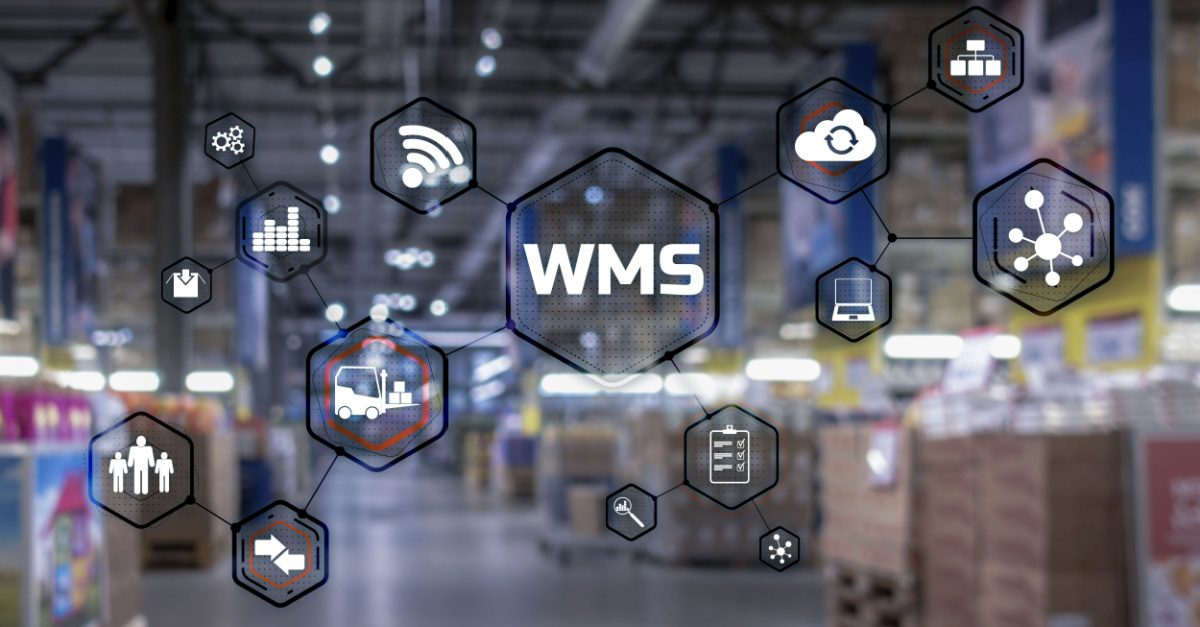
4 Warehouse Management Problems And Their Solutions
You may encounter challenges when managing your warehousing operations. They may impact the efficiency and speed of your production line, resulting in low cash flow and higher production costs. In most cases, it’s challenging to identify warehouse problems unless you initiate the process. And by then, it might be too late to prevent the error or reduce the damage done. However, understanding the issues you might encounter in your warehouse may help avoid them and reduce their impact. Here are 4 Warehouse Management Problems and their solutions.
This blog covers some warehouse management challenges you might encounter and what you can do to stay clear of them.
Disorganised Warehouse Layout
It’s crucial to use the available space efficiently when managing a warehouse. Otherwise, the workforce may spend too much time moving from one point to another. Also, it might be challenging for forklifts to reach certain products, or you may forget certain pallets. In other words, your operations can be severely jeopardised, and you’ll lose money in the long run.
However, you can avoid this by taking advantage of vertical floor space. This makes it easier to maintain pallet racking to facilitate effective offloading and unloading of products. Additionally, you should sort your products based on popularity or seasonality. Hence, the team members will know where to look, saving them considerable time.
Image by: Bowenstorage |Maintain pallet racking
Another solution to the above challenge is a warehouse management system (WMS). It’s a tool that helps warehouse managers track all products that come in and out of the warehouse. It also gathers crucial data such as stock-keeping units (SKUs), making it easier to decide where goods should be placed. A WMS makes it easier and more efficient to fulfil your orders, boosting customer experience and increasing your cash flow.
Bad Inventory Management
There are several signs you have bad inventory management:
- You expect to find a product in a specific location, only to realise it’s stored elsewhere.
- You accept an order thinking you have enough stock to fulfil it, only to find out later that you don’t. You’ll be forced to place a backorder, which could affect customer experience. On the other hand, you may deny an order assuming you don’t have enough stock.
The above signs indicate that you don’t have an accurate inventory record. This could lead to lost sales, poor customer experience, and public image.
One of the significant causes of lousy inventory is manual processes. When you’re checking your list manually, there are high chances of making an error. It can also happen when you’re using obsolete systems.
Therefore, consider utilising newer and digital solutions to overcome this warehouse challenge. A modern inventory management tool will track and record data in real time; thus, you’ll know what products you have in stock and which ones you should restock. Also, you can prevent issues such as missed sales, uncertain cashflows, and higher holding costs.
Doing Redundant Tasks
Each product in a warehouse has several tasks done on it, from the moment it enters the warehouse till it leaves. The problem starts when two or more people do the same task, leading to redundancy. This results in time and resource wastage, affecting your overall profit margin. The intensity of this issue varies, and it’s more profound in large warehouses.
However, you can avoid the above challenge by increasing resource visibility. There are several ways you can achieve this, including the following:
- Use barcodes – These tools will help you automate inventory management. Thus, knowing where each item is located will be easier, reducing inventory redundancy. Additionally, barcode systems help increase picking accuracy and customer experience.
- ABC analysis – This strategy ensures you can easily access popular or fast-moving items. On the other hand, slow-moving products are stored in the back of the warehouse. As a result, you fulfil orders quickly and efficiently.
Another way to address redundancy is by employing cloud systems. Cloud computing allows the involved parties to access the needed updates, regardless of the location. Thus, team members will know which departments work on specific operations, hence avoiding doing similar tasks on a product.
Excessive Spending On Labour
Your workforce plays a huge role in ensuring that the warehouse operations run smoothly. However, spending too much on them will affect your profit margin. Thus, developing a deeper insight into your labour is crucial.
First, start by reviewing all the labour in your warehouse. Then look at the systems you’re already using; through this, determining whether you need to automate more tasks will be easier. You can also partner with another business to save warehouse space and reduce labour costs.
Bottom Line
As a warehouse manager, you may encounter several challenges, including a disorganised layout, redundant operations, and a costly workforce. These issues may affect the overall efficiency of your warehouse operations. Hence, it’s crucial to identify the right strategies to address them.
As with most supply chain sectors, the roles and responsibilities of those in an Warehousing and Operations position can be varied. IoSCM’s Warehousing Academy enables those in industry to develop their skills through bespoke distance learning courses.