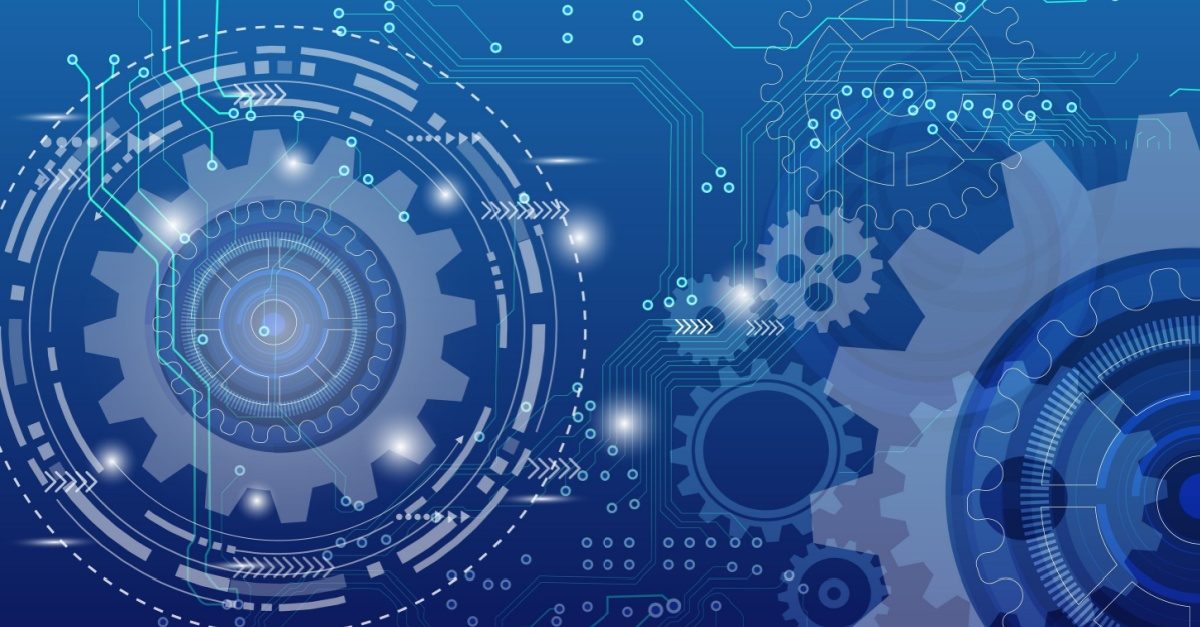
How To Choose The Right Precision Gears For Your Industrial Equipment
Precision gears play a vital role in the smooth operation of industrial equipment. These gears control motion, manage force, and influence the speed of machines in various settings—from manufacturing plants to robotic arms. Choosing the right type can improve efficiency, reduce wear and tear, and extend equipment life. With many options available, selecting the right gear requires more than guesswork. It involves understanding the application, the environment, and the technical features that affect performance. This guide breaks down the key factors to consider when making a decision.
Understand What the Gear Needs to Do
The first step is understanding the gear’s purpose and working conditions. Will it handle heavy loads or operate at high speeds? Is it going to be exposed to heat, chemicals, or moisture? Will it run continuously or only at intervals? These questions help define what kind of gear is best suited for the task.
For instance, a gear used in a packaging machine may require quiet operation and high precision, while one in a construction device must endure constant pressure and harsh outdoor conditions. Outlining the gear’s function early on avoids costly mismatches and system failures later.
Choose the Gear Type That Fits the Job
Precision gears come in several types, each built for specific roles. Knowing their basic characteristics helps match them with the right machinery:
- Spur gears: These have straight teeth and are easy to manufacture. They are efficient for lower-speed, lower-load tasks.
- Helical gears: With slanted teeth, these run more quietly and smoothly than spur gears. They’re suited for high-speed and high-load applications.
- Bevel gears: These transfer motion between shafts that intersect, usually at a 90° angle. They are common in automotive systems and industrial tools.
- Worm gears: These use a screw-like design to achieve large reductions in speed. They’re useful when compact design and self-locking features are required.
Each type offers distinct advantages. For example, helical gears may be more costly than spur gears, but they reduce noise and wear over time, making them a better fit for high-performance systems. Many of these gear types can be found online from trusted sources like ntgear.co.uk, which offers a range of precision gears suitable for different industrial needs.
Pick the Right Material
The material of the gear influences its strength, lifespan, and compatibility with the environment. Choosing the wrong one could lead to failure or inefficient performance.
- Steel: Strong and durable, making it ideal for high-load, high-speed operations. Often used in machinery that runs continuously.
- Brass: Quieter and more resistant to wear than steel, but not as strong. Often chosen for precision tasks where silence matters.
- Plastic (such as nylon or acetal): Lightweight and resistant to corrosion. Suitable for clean environments or equipment with low stress.
- Aluminium: Light and rust-resistant, though softer and less wear-resistant than steel.
For example, plastic gears are commonly used in laboratory equipment due to their quiet operation and cleanliness, while steel gears are standard in manufacturing lines where strength and durability are priorities.
Pay Attention to Precision and Tolerances
High-precision gears are manufactured to exact standards. Even a slight deviation in shape, size, or spacing can cause vibration, excess noise, or breakdowns—especially in machines that depend on accurate motion.
Tight tolerances ensure the gear teeth mesh properly with their counterparts. This is particularly important in equipment like automated packaging systems or robotic joints, where any misalignment can interrupt the process or damage parts.
Consider Heat Treatment and Coatings
Some gears undergo heat treatment to improve their hardness, which allows them to withstand more stress and last longer. Others receive surface coatings—such as zinc plating or black oxide—to resist corrosion and minimise friction.
These enhancements are especially important in environments exposed to chemicals, water, or frequent cleaning. For example, food and beverage processing equipment often uses coated gears to maintain hygiene and prevent rust during washdowns.
Match the Gear With the System
A gear must integrate smoothly with other machine components. Mismatches in size, shaft alignment, or torque requirements can lead to mechanical issues or reduced efficiency.
Always confirm that the gear’s specifications match the gearbox or system it’s part of. If in doubt, consult with the machine’s manufacturer or a gear specialist to ensure compatibility and avoid future maintenance headaches.
Balance Cost With Long-Term Value
Precision gears come at a range of prices, and while staying within budget matters, it’s also important to consider long-term costs. Cheap, low-quality gears may wear out quickly, break more easily, or affect other components, leading to frequent replacements or downtime.
Investing in higher-quality gears may cost more upfront but can result in greater reliability, less maintenance, and better performance over time—especially in machines that operate around the clock or under demanding conditions.
Look for Quality Standards
Reliable gears often come with certifications that show they meet industry standards, such as ISO or AGMA ratings. These certifications indicate the gear has been tested for durability, accuracy, and performance.
When gears are used in high-precision environments—like aerospace, medical devices, or automated production—choosing certified components adds a layer of confidence and helps meet regulatory requirements.
Conclusion
Choosing the right precision gear involves more than selecting a size or shape. It requires a clear understanding of the equipment’s purpose, the conditions it will face, and how the gear fits into the entire system. By evaluating the gear type, material, accuracy, treatments, and compatibility, businesses can ensure smoother operation, reduce the risk of breakdowns, and increase long-term efficiency. A well-chosen gear not only supports the machinery but also helps maintain consistent performance in demanding industrial settings.
From introductory production planning and scheduling training to advanced types of manufacturing operations, the IoSCM Manufacturing and Production Academy offers manufacturing qualifications from Level 2 to Level 7. Speak with a Course Advisor to find out how we can help you.