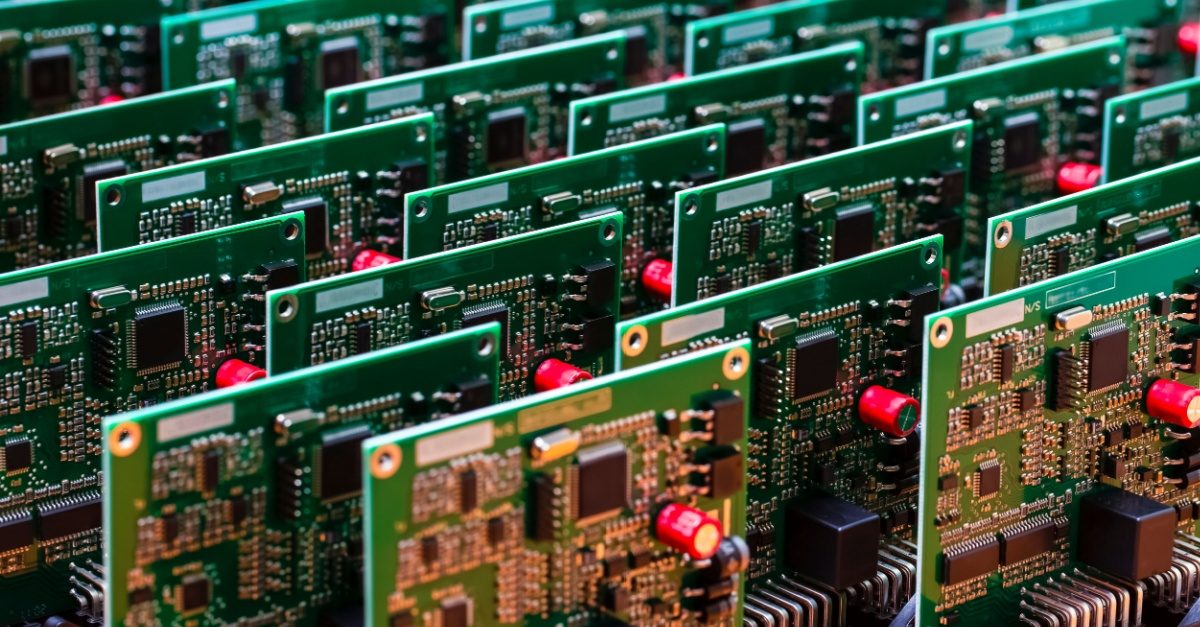
Soldering vs. Crimping: Which One Is Best for Your Project?
When it comes to working with electrical wiring or metal components, choosing the right connection method can make or break the durability, safety, and reliability of your project. Soldering and crimping are two of the most common approaches. But how do you know which technique will best serve your needs? Let’s unpack this decision step by step with expert-level insights and practical advice.
Understanding Soldering: Why Precision and Permanence Go Hand in Hand
Imagine assembling a complex circuit where every connection must hold firm without a millimeter of movement. This is where soldering comes into play.
In soldering, you melt a metal alloy-typically a mixture of tin and lead or a lead-free alternative such as tin-copper – to create a strong, conductive bond between wires or components. Once cooled, this bond becomes a permanent fixture that resists detachment.
What makes soldering essential in certain projects?
- Electrical continuity: Solder fills microscopic gaps between metal surfaces, ensuring optimal current flow without interruptions. In high-frequency circuits, for example, even small disruptions can cause signal degradation. Soldered joints typically exhibit electrical resistance below 0.01 ohms when properly made.
- Compact, custom fits: When dealing with intricate projects, like custom PCB (printed circuit board) work, soldering allows for tight, space-efficient joints. For instance, components on a microcontroller require precise soldering to avoid bridging – an accidental connection between two points, which can short-circuit the board.
- Vibration resistance (when done correctly): In sensitive electronics, solder joints reduce micro-movement between components. For example, aerospace technicians solder critical circuit assemblies but use flux carefully to minimise residue that could trap moisture or dust over time. Solder joints in aerospace systems may need to withstand vibration levels exceeding 20 g (gravitational force).
However, soldering requires mastery to avoid pitfalls. Overheating wires can damage insulation and weaken conductivity. Cold solder joints – formed when the solder doesn’t fully melt – appear dull and brittle, often causing intermittent connectivity issues.
Advanced tip: Use a temperature-controlled soldering iron, typically set between 315°C and 370°C, and practice using different tips (chisel, conical) to match wire or terminal sizes. A proper preheating step also prevents heat shock when working with fragile materials (source).
If your work demands precision and minimal movement, soldering is indispensable. Still, what if your project requires something more adaptable?
Crimping: The Champion of Durability and Speed
Think about the last time you wired a set of speakers or installed a new light fixture. You probably relied on crimping. Crimping involves compressing a metal connector onto a wire using specialised tools, forming a mechanically secure bond that doesn’t require heat. In high-production environments like automotive assembly lines, crimping is a go-to technique for both speed and consistency.
Why do professionals swear by crimping for certain applications?
- Speed and efficiency: In a single press, a crimping tool delivers a fully formed connection. This can reduce assembly time dramatically – critical for large projects or time-sensitive repairs. Industrial-grade crimping can take as little as 2 seconds per terminal, compared to soldering times of 15–60 seconds per joint.
- Mechanical strength: A properly crimped terminal can withstand significant pulling forces without failure. For instance, crimped automotive connectors are designed to endure tensile forces of 20–30 pounds without detachment.
- Environmental resilience: Crimped joints excel in harsh conditions. Waterproof or heat-shrink crimp terminals, for example, seal out moisture and corrosion, making them ideal for marine and automotive wiring harnesses. High-performance crimped connections may pass environmental tests such as MIL-STD-810 (military standard) for temperature and moisture.
Yet, improper crimping can cause major issues. Loose connections lead to arcing – dangerous sparks caused by unstable electrical contact – while over-crimping damages wire strands, reducing load capacity.
Advanced tip: Always match the crimp terminal size to the wire gauge (AWG) and use ratcheting crimp tools to ensure even pressure. For example, a 16 AWG wire typically requires a red-insulated terminal with a wire barrel diameter between 1.5 mm and 2.5 mm.
Need a fast, rugged solution that withstands rough conditions? Crimping might just be your project’s secret weapon. But how do soldering and crimping stack up in terms of longevity?
Tool Talk: What Equipment Will You Need?
Investing in proper tools elevates your work from hobbyist to professional grade. Here’s a breakdown:
For soldering:
- Temperature-controlled soldering station with interchangeable tips, capable of maintaining between 300°C and 400°C.
- Lead-free solder wire with rosin core (for flux) in diameters ranging from 0.5 mm to 1.2 mm for different project needs.
- Soldering accessories like fume extractors and helping hands to prevent fatigue.
For crimping:
- Ratcheting crimp tool for consistent pressure, often adjustable for various terminal types.
- Terminals sized for your wire gauge, with insulation colors coded (red for 22–18 AWG, blue for 16–14 AWG, and yellow for 12–10 AWG).
- Wire strippers to ensure clean wire ends before crimping.
Where to buy crimping tools? A great option is Maun Industries. Maun’s range of crimping tools are reliable and very well made.
Pro tip: Avoid bargain-bin tools. Inconsistent pressure from low-quality crimpers or poorly regulated soldering irons leads to substandard results. Well-made tools will pay for themselves in reliability.
Equip yourself with quality tools for frustration-free work. Next, let’s look at common mistakes and how to troubleshoot them.
Which One Offers Better Long-Term Reliability?
You might be wondering: which method will last longer in my project? The answer depends largely on the environment, stress factors, and materials used.
When soldering excels:
- Stable environments: Indoor projects with controlled temperatures benefit from solder’s excellent electrical properties. Home automation systems, for instance, often use soldered joints on control boards to maintain consistent connectivity over years.
- High-precision electronics: Devices where even minor electrical resistance affects performance – such as audio amplifiers or RF (radio frequency) communication systems – rely on solder to maintain clean, noise-free connections. In such applications, resistance increases as little as 0.001–0.005 ohms can degrade performance.
When crimping takes the lead:
- Dynamic environments: Projects involving constant motion or vibration, such as a car’s wiring harness, fare better with crimping. Soldered joints may develop stress fractures over time due to mechanical fatigue (source).
- Exposure to the elements: Outdoor security systems or solar installations require connections that won’t corrode or degrade. Crimping with sealed connectors prevents moisture ingress, a common culprit of solder failure. Terminals rated for IP67 (ingress protection) offer excellent sealing for these environments.
Advanced insight: Combine techniques where appropriate. Use soldering for PCB work, but crimp connections where wires exit enclosures to balance strength and electrical integrity.
Consider your project’s environment carefully. If extreme conditions are in play, crimping often proves superior in maintaining long-term performance.
Ease of Use: Which Technique is More Beginner-Friendly?
Both soldering and crimping require practice, but their learning curves differ significantly.
Soldering requires:
- Heat management: Excessive heat damages insulation, while insufficient heat causes weak bonds. A beginner might struggle to find this balance without guided practice.
- Steady hand and patience: Even minor movements while soldering can lead to imperfect joints, particularly on delicate projects like circuit boards.
Crimping demands:
- Tool familiarity: Different tools and connectors cater to specific wire gauges and terminal types. Beginners often benefit from ratcheting crimpers that provide tactile feedback when the crimp is complete.
- Correct sizing: Misjudging the wire-to-connector fit can compromise the connection’s integrity.
Many DIYers find crimping more approachable since there’s less risk of damage from overheating. Still, mastering soldering enhances your versatility, especially for detailed electronic work.
Pro tip: Create a practice board with spare wires to experiment with both techniques before tackling your main project. Use wires of varying sizes, such as 12 AWG for higher current applications and 22 AWG for finer electronics, to understand how each method performs.
If you’re new to wiring, crimping offers faster, more forgiving results. Soldering, however, rewards patience with precision craftsmanship.
Troubleshooting Tips: Avoiding the Most Common Pitfalls
No method is immune to errors, but recognising them early can save hours of rework.
Soldering issues:
- Cold joints: These appear dull and lack strength. Increase the temperature or apply flux to promote full melting.
- Overheating: Signs include scorched insulation or wire brittleness. Use heat sinks on sensitive components to prevent damage.
Crimping issues:
- Loose crimps: Ensure even pressure with the correct tool for your terminal type.
- Damaged wires: Over-crimping cuts into strands, weakening electrical flow. Avoid excess force.
Advanced troubleshooting: Inspect connections with a multimeter. High resistance readings often indicate weak solder joints or poorly crimped terminals. Aim for resistance values below 0.1 ohms for optimal performance.
A little prevention goes a long way. Regular inspection and testing keep your project on track.
At the Institute of Supply Chain Management (IoSCM), we offer a range of bespoke manufacturing courses which can help you take the next step in your career. Our unique and innovative approach allows each learner to use their practical work experience towards accredited industry-recognised qualifications. The IoSCM Manufacturing and Production Academy offers manufacturing qualifications from level 2 right up to level 7, so we’ve got you covered for every step of your career development.